經典案例
圓形的工作臺邊,幾個人組成的工作單元完成全部的組裝工作。沒有了流水線,沒有了無人幫運機,也不見了自動化倉庫,單元式生產開始成為佳能新的選擇。
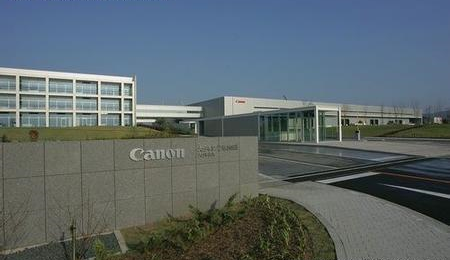
社長俯身求教
“一提起降低成本,似乎馬上就想到產業外輸化,但是這樣做不過是利用了外輸地優越的生產條件,公司本身的生產力并沒有改進。”每次回國,看到本國公司空洞化,工廠一片慘淡的情形,痛心而由衷地期望進行一次能夠真正提高佳能生產效率的革新。
他仔細地分析了當前的困境:面對產品更新換代加快,品種日趨多樣化的勢頭,以少品種、大產量為前提的流水線生產方式開始顯得捉襟見肘,它不僅僅會導致銷售機會喪失,還有可能陷入大量庫存的危機。如果一味依賴巨額投資的大型生產設備,投資調配就會出現困難。
所以,尋找一種靈敏的、富有彈性的、能夠滿足小產量、多品種要求的生產方式,成了佳能最迫切的希望。
此時,一家電子零部件廠的代表團來佳能參觀,他們對佳能的自動化流水線給予了毫不留情的批評:“這些長長的傳送帶根本就沒必要,佳能完全是在浪費錢”,“把‘無人幫運’這種無聊的東西都合理化了,再也找不到這樣愚蠢的事了。”
面對如此辛辣的批評,社長決定和各位董事一起看看那家電子零部件工廠和一家大型電機制造工廠。他們驚奇地發現對方已經停止了傳送帶流水作業方式,采取了一種新的、被稱為“單元生產”的生產方式--由幾個人組成的生產小組從事全部復雜工程,生產出完整產品。
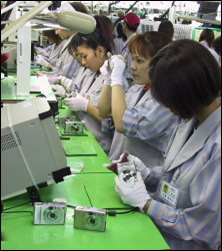

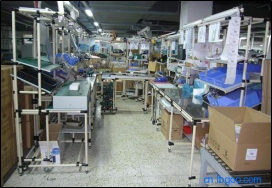

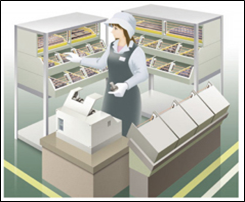
比如日本市場曾經流行的超薄翻蓋手機P504i的組裝就采用了單元式生產方式。3名女工站在不到3米長的工作臺前組成一個單元,所有的手機裝配流程都由她們完成。第一名女工的工作是把一塊電路板裝進上蓋板,裝好攝像頭,擰緊螺絲,完成后放到第二名女工的手邊;第二名女工用聯線把上下蓋板連接起來,傳給第三名女工,同時順手幫她拿上一塊電路板;第三名女工把電路板裝進下蓋板,擰好螺絲,手機裝配完成。整個過程不到半分鐘,這樣一個單元一天可裝配手機900部,而以前一條流水線需要14個人作業,每天只能生產1300部。所需零部件都堆放在工作臺上,工人不用移動位置,這就減少了機器、半成品和人員移動的損耗。而且還大大節約了空間,裝配車間的1/3因此空閑下來。
在參觀完工廠后,社長決定從長浜佳能開始進行生產革新。1998年初,革新運動正式開始。
表面看來,單元式生產方式對流水線生產方式的否定是生產流程技術性的變化。實質上,這是一種制度創新,是生產觀念的革新。單元式生產方式并不像流水線生產方式那樣,需要高度的機械化和自動化的流水線,而且很多人也知道這樣一種方法,但是為什么大多數人都不愿意去實踐呢?因為過去流水線生產方式取得了輝煌的成功。大多數企業被“福特主義”神話所束縛,像佳能這種不斷擴大、發展的公司,大型的流水線生產還是一種發展、進步和實力的象征。
然而這一思維卻忽略了當今時代個性化需求所帶來的巨大變化。佳能從現金流通經營方面考慮,把那些固定大量資金的重、厚、長、大的設備、庫存品、半成品視為“惡”,對于樣品變更反應遲鈍的生產方式也視為“惡”,由于生產過剩將多余的庫存品強塞給銷售公司來提高銷售額的做法更是“惡的極至”。所以,當他發現單元式生產方式后,就毫不猶豫地對傳統的流水線生產方式進行了質疑,分析認為:雖然像汽車這樣大型產品的組裝,單元式生產方式顯得有些力不從心,但對于復印機這類產品而言,單元式生產方式加以改進是非常合適的。
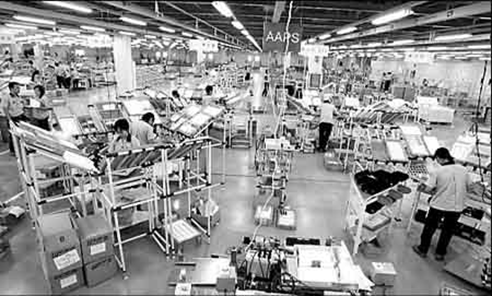
流水線撤除行動
“如果生產革新一開始就在整個公司展開,可能會引起強烈的反對,反而會有失敗的危險。”考慮到這一點,社長決定從首先提出改革方案的周邊機器事業總部開始改革。
但了解到當時生產總部正在進行“新佳能生產系統的革新運動”,并且取得了一定成果。如果現在馬上叫他們進行單元式生產變革,恐怕很難有回應。于是,他干脆避開了總公司的工廠,而把子公司長浜佳能作為了改革的“先頭部隊”,采用先從周邊工廠點燃火種,再擴展到整體的戰略。
長浜佳能的生產部長考慮到革新的困難,決定采取逐步推進的方式,從“節省空間”運動切入。
于是他們除去流水線上多余的動作以及生產現場利用無人運送機搬運零件等無用環節。一方面減少了流水線作業者之間的距離,另一方面重新安排工廠的陳設,縮短零件移送的距離,這樣一來作業者就不會過于枯燥,工作效率也提高了。由于工廠節約出很多的空間,原本安置在別處的捆包生產線也搬到了激光打印機主機組裝生產線的旁邊,兩者結合使得作業效率一下子提升了。
與此同時,生產主要零件的流水線組裝方式向單元式轉換的試驗也正式開始。為了降低風險,長浜佳能決定從相對簡單的激光掃描儀組裝生產線開始。因為激光掃描儀組裝生產線只有20米,是掃描儀生產線的1/10。
單元式生產進一步縮短了激光掃描儀生產線的距離,以前20米長的流水生產線,現在只用10米長就可以,實際上,相同生產線的產量就是過去的2倍;另外,兩邊堆放的物料也縮短一半,節省了產品停留在傳送帶上的時間,節省了整體成本,提高了效率。而且,工廠管理人員、監督人員和技術人員以3個月為一個周期對有浪費的環節進行改善。
當初步的試驗順利進行的時候,打印機主機組裝生產線的試驗也同步開始。他們不是一口氣急于將6條生產線一次性地轉為單元式,而是一條一條依次進行變更,也不是極端地采用一個人為一個單元的方式,而是改成10個人一個小組進行作業。
試驗開始得并不順利,從各種數據看,生產效率不僅沒有明顯提高,反而有所降低。但是“救命女神”最終出現了。生產現場的女工組成了一個10人女性生產小組,她們在每次作業結束后,自主地召開一個小型討論會,摸索改善的方法。與此同時,現場生產的工人們盡管有所不滿,但也漸漸地熟悉了這種作業方式,生產現場開始出現工人積極工作的氛圍。在連續召開三天討論會后,女性生產小組終于提前完成了生產任務,受到她們的激勵,其他現場的工人也開始積極地投入工作。
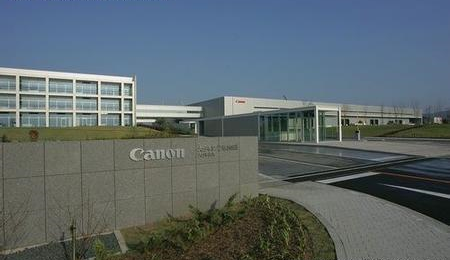
社長俯身求教
“一提起降低成本,似乎馬上就想到產業外輸化,但是這樣做不過是利用了外輸地優越的生產條件,公司本身的生產力并沒有改進。”每次回國,看到本國公司空洞化,工廠一片慘淡的情形,痛心而由衷地期望進行一次能夠真正提高佳能生產效率的革新。
他仔細地分析了當前的困境:面對產品更新換代加快,品種日趨多樣化的勢頭,以少品種、大產量為前提的流水線生產方式開始顯得捉襟見肘,它不僅僅會導致銷售機會喪失,還有可能陷入大量庫存的危機。如果一味依賴巨額投資的大型生產設備,投資調配就會出現困難。
所以,尋找一種靈敏的、富有彈性的、能夠滿足小產量、多品種要求的生產方式,成了佳能最迫切的希望。
此時,一家電子零部件廠的代表團來佳能參觀,他們對佳能的自動化流水線給予了毫不留情的批評:“這些長長的傳送帶根本就沒必要,佳能完全是在浪費錢”,“把‘無人幫運’這種無聊的東西都合理化了,再也找不到這樣愚蠢的事了。”
面對如此辛辣的批評,社長決定和各位董事一起看看那家電子零部件工廠和一家大型電機制造工廠。他們驚奇地發現對方已經停止了傳送帶流水作業方式,采取了一種新的、被稱為“單元生產”的生產方式--由幾個人組成的生產小組從事全部復雜工程,生產出完整產品。
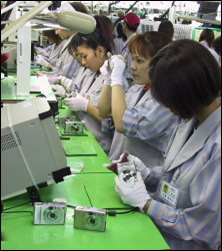

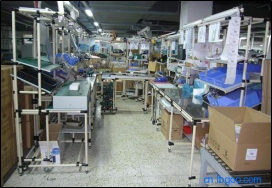

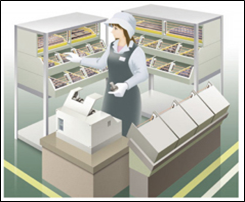
比如日本市場曾經流行的超薄翻蓋手機P504i的組裝就采用了單元式生產方式。3名女工站在不到3米長的工作臺前組成一個單元,所有的手機裝配流程都由她們完成。第一名女工的工作是把一塊電路板裝進上蓋板,裝好攝像頭,擰緊螺絲,完成后放到第二名女工的手邊;第二名女工用聯線把上下蓋板連接起來,傳給第三名女工,同時順手幫她拿上一塊電路板;第三名女工把電路板裝進下蓋板,擰好螺絲,手機裝配完成。整個過程不到半分鐘,這樣一個單元一天可裝配手機900部,而以前一條流水線需要14個人作業,每天只能生產1300部。所需零部件都堆放在工作臺上,工人不用移動位置,這就減少了機器、半成品和人員移動的損耗。而且還大大節約了空間,裝配車間的1/3因此空閑下來。
在參觀完工廠后,社長決定從長浜佳能開始進行生產革新。1998年初,革新運動正式開始。
表面看來,單元式生產方式對流水線生產方式的否定是生產流程技術性的變化。實質上,這是一種制度創新,是生產觀念的革新。單元式生產方式并不像流水線生產方式那樣,需要高度的機械化和自動化的流水線,而且很多人也知道這樣一種方法,但是為什么大多數人都不愿意去實踐呢?因為過去流水線生產方式取得了輝煌的成功。大多數企業被“福特主義”神話所束縛,像佳能這種不斷擴大、發展的公司,大型的流水線生產還是一種發展、進步和實力的象征。
然而這一思維卻忽略了當今時代個性化需求所帶來的巨大變化。佳能從現金流通經營方面考慮,把那些固定大量資金的重、厚、長、大的設備、庫存品、半成品視為“惡”,對于樣品變更反應遲鈍的生產方式也視為“惡”,由于生產過剩將多余的庫存品強塞給銷售公司來提高銷售額的做法更是“惡的極至”。所以,當他發現單元式生產方式后,就毫不猶豫地對傳統的流水線生產方式進行了質疑,分析認為:雖然像汽車這樣大型產品的組裝,單元式生產方式顯得有些力不從心,但對于復印機這類產品而言,單元式生產方式加以改進是非常合適的。
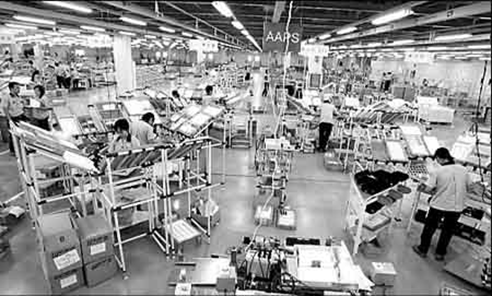
流水線撤除行動
“如果生產革新一開始就在整個公司展開,可能會引起強烈的反對,反而會有失敗的危險。”考慮到這一點,社長決定從首先提出改革方案的周邊機器事業總部開始改革。
但了解到當時生產總部正在進行“新佳能生產系統的革新運動”,并且取得了一定成果。如果現在馬上叫他們進行單元式生產變革,恐怕很難有回應。于是,他干脆避開了總公司的工廠,而把子公司長浜佳能作為了改革的“先頭部隊”,采用先從周邊工廠點燃火種,再擴展到整體的戰略。
長浜佳能的生產部長考慮到革新的困難,決定采取逐步推進的方式,從“節省空間”運動切入。
于是他們除去流水線上多余的動作以及生產現場利用無人運送機搬運零件等無用環節。一方面減少了流水線作業者之間的距離,另一方面重新安排工廠的陳設,縮短零件移送的距離,這樣一來作業者就不會過于枯燥,工作效率也提高了。由于工廠節約出很多的空間,原本安置在別處的捆包生產線也搬到了激光打印機主機組裝生產線的旁邊,兩者結合使得作業效率一下子提升了。
與此同時,生產主要零件的流水線組裝方式向單元式轉換的試驗也正式開始。為了降低風險,長浜佳能決定從相對簡單的激光掃描儀組裝生產線開始。因為激光掃描儀組裝生產線只有20米,是掃描儀生產線的1/10。
單元式生產進一步縮短了激光掃描儀生產線的距離,以前20米長的流水生產線,現在只用10米長就可以,實際上,相同生產線的產量就是過去的2倍;另外,兩邊堆放的物料也縮短一半,節省了產品停留在傳送帶上的時間,節省了整體成本,提高了效率。而且,工廠管理人員、監督人員和技術人員以3個月為一個周期對有浪費的環節進行改善。
當初步的試驗順利進行的時候,打印機主機組裝生產線的試驗也同步開始。他們不是一口氣急于將6條生產線一次性地轉為單元式,而是一條一條依次進行變更,也不是極端地采用一個人為一個單元的方式,而是改成10個人一個小組進行作業。
試驗開始得并不順利,從各種數據看,生產效率不僅沒有明顯提高,反而有所降低。但是“救命女神”最終出現了。生產現場的女工組成了一個10人女性生產小組,她們在每次作業結束后,自主地召開一個小型討論會,摸索改善的方法。與此同時,現場生產的工人們盡管有所不滿,但也漸漸地熟悉了這種作業方式,生產現場開始出現工人積極工作的氛圍。在連續召開三天討論會后,女性生產小組終于提前完成了生產任務,受到她們的激勵,其他現場的工人也開始積極地投入工作。
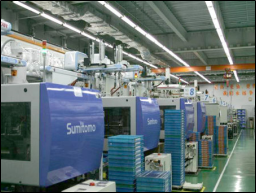
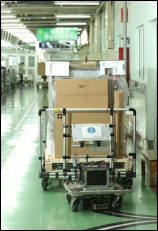